En fecha tan reciente como los años 90, los incrédulos reían sin piedad de las predicciones de futurólogos que confiaban en que pronto habría impresoras para manufacturar productos físicos bajo demanda a partir de un diseño computerizado, tales como microchips o juguetes (así lo hacía, por ejemplo, Nicholas Negroponte en su ensayo Being Digital —1995—).
Estas impresoras de objetos, surgidas en los 80, lograban resultados modestos y toscos, pero una analogía con la rápida evolución de, por ejemplo, el ritmo de miniaturización de los microprocesadores (Ley de Moore), invitaba al optimismo en círculos especializados.
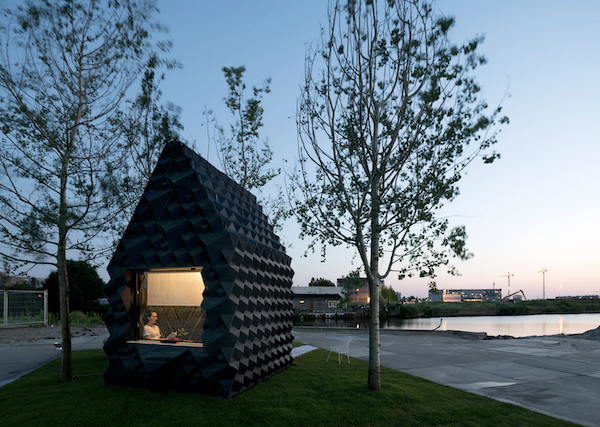
Sobre el papel, las impresoras 3D contaban con una ventaja esencial con respecto a otras técnicas para fabricar objetos físicos de uso profesional y amateur: imprimir es un proceso aditivo, en el que únicamente se emplea el material requerido para concebir una tarea, mientras que en técnicas substractivas como el fresado de control numérico («CNC milling»), el objeto se define al substraerlo de una pieza de material de mayor tamaño, con el derivado malgasto en material sobrante.
Larga trayectoria de una técnica prometedora
La impresión 3D tenía, por tanto, sentido. A la larga, pensaron los analistas, una técnica aditiva suficientemente flexible reduciría el malgasto de energía y material que requieren los métodos de fabricación extractivos. Pero el recorrido desde los postulados teóricos a los prácticos se está revelando complejo y arriesgado, tanto para los aficionados como para los inversores privados e institucionales.
Asimismo, si la tecnología se convertía en un medio periférico más de la informática profesional y doméstica, tal y como había ocurrido con la impresora a papel, pronto pequeños talleres y aficionados serían capaces de producir sus propios productos bajo demanda, lo que eliminaba la necesidad de acumular inventario y apostarlo todo a la producción centralizada, según el modelo de las economías de escala.
Dos décadas después de su estreno comercial, las impresoras 3D siguen siendo una promesa, pero apenas han encontrado aplicaciones a gran escala que puedan competir con metodologías industriales consolidadas durante décadas.
Además del prototipado rápido, en la pasada década avanzó la fabricación aditiva para prótesis, medicamentos adaptados al paciente, reconstrucciones anatómicas y de órganos; también han madurado aplicaciones en automoción (piezas de recambio a bajo coste), moda (calzado de altas prestaciones, complementos), así como la aeronáutica.
Como siempre, la posibilidad técnica debería supeditarse al interés del mercado o a efectos aceleradores de tendencias como una emergencia a gran escala (por ejemplo, el efecto de una pandemia como la actual sobre el interés de empresas y aficionados para desarrollar piezas y material sobre la marcha).
Constructoras que son tecnológicas
Durante la década pasada, las impresoras 3D mejoraron sus prestaciones a la vez que reducían su tamaño y costo, pero los primeros modelos asequibles orientados a un consumidor no especializado apenas lograban justificar la inversión con un puñado de aplicaciones prácticas todavía en ciernes. Sin embargo, la «Revolución Industrial» que debían haber producido debe relativizarse.
Varias empresas tratan de superar las limitaciones técnicas y regulatorias para, por ejemplo, imprimir carrocerías de automóvil, fuselajes aeronáuticos o incluso viviendas, y las impresoras actuales imprimen con mayor rapidez y precisión objetos más grandes y en materiales cada vez más específicos.
En varios mercados especializados, hace mucho tiempo que las impresoras 3D han dejado de ser un juguete caro o un método alternativo a los artesanales para prototipos rápidos y moldes para crear objetos de plástico o silicona natural.
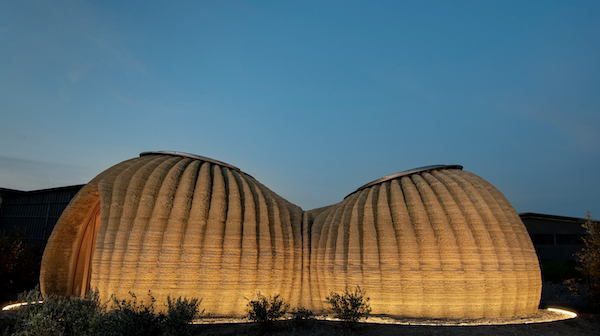
Pese a sus atavismos y dependencia burocrática, el sector de la construcción no es ajeno a la promesa de la fabricación aditiva. Recientemente, en *faircompanies aprovechamos nuestra estancia en la bahía de San Francisco para visitar la sede de una de las empresas que trata hacer realidad la impresión de viviendas, Mighty Buildings. La arquitectura y el diseño industrial y de mobiliario realizan ahora la transición desde el uso marginal de la tecnología en prototipado a la fabricación de componentes o incluso estructuras bajo demanda.
Mighty Buildings es una de las muchas empresas que tratan de abaratar y reducir el impacto de la construcción residencial, a la vez de acelerar procesos al reducir su dependencia del trabajo manual local, cuya escasez crónica en regiones como California se acrecienta ahora con la reconstrucción de viviendas destruidas por los incendios veraniegos de los últimos años.
El reto de imprimir casas bajo demanda
La visita a esta empresa nos evocó otras excursiones realizadas con anterioridad a la sede y taller de dos empresas todavía en ciernes hace poco más de una década: Zero Motorcycles, el fabricante de motos de Santa Cruz; y la primera sede de Tesla en El Camino Real, la arteria viaria del valle de Santa Clara.
Entonces, ambas empresas fabricaban sus respectivos vehículos por encargo y dependían del interés de inversores y un puñado de entusiastas pioneros, si bien la realidad es hoy muy distinta y hasta Harley Davidson o Ford apuestan per una plataforma motriz eléctrica. O expresado por Hemingway en su novela Fiesta (a propósito de un personaje que explica cómo se ha arruinado), cualquier cambio se produce primero lentamente, hasta que llegado el momento todo parece ocurrir de sopetón.
Mighty Buildings se encuentra en una desangelada zona industrial de Oakland, al este de la Bahía de San Francisco, donde ocupa una generosa porción de una nave con más inquilinos.
Visita a Mighty Buildings
Durante nuestra visita de mediados de agosto, entramos en unas oficinas que tienen poco que ver con el entorno que suele rodear las empresas de construcción tradicionales: los puestos administrativos y de computación ocurren a un lado de las instalaciones, mientras una pequeña sala asiste al visitante a cambiar de contexto como lo haría un astronauta al aguardar en la sala de descompresión, y al otro lado se extiende el lugar de fabricación de las viviendas que la empresa pretende imprimir bajo demanda.
Al fondo de la generosa nave industrial, varios operaros se apresuran con los acabados exteriores e interiores de pequeñas viviendas con fachada acristalada. La estructura de estas casas, algunas de las cuales son viviendas en toda regla y otras pretenden competir en el mercado de las casitas accesorias (ADU en sus siglas en inglés, un tipo de edificio accesorio legalizado en California) en plena crisis inmobiliaria, ha sido impresa en un hangar anejo con lo que parece la versión gigante de una impresora 3D convencional.
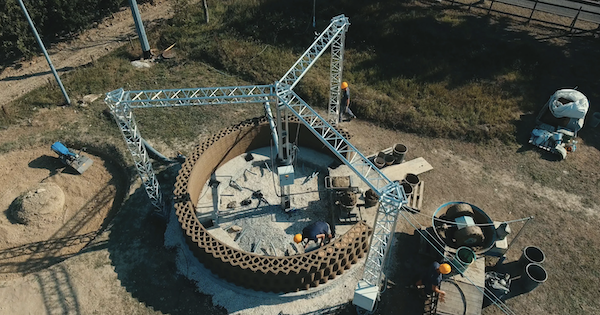
Realizamos un recorrido por las instalaciones y preguntamos sobre la materia prima de la que se sirve la impresora para depositar con precisión cada una de las capas superpuestas que aumentan visiblemente de tamaño durante el paseo; el objetivo, nos dicen, es crear materiales con prestaciones cada vez más adecuadas, con mayor resistencia y menor impacto, si bien hay que conformarse de momento con un mortero sintético cuyo producto esencial es la piedra caliza.
Impresoras 3D y el contexto de la vivienda
Mighty Buildings es una de las empresas que tratan de modernizar un mercado hasta ahora impermeable a la evolución tecnológica: la construcción residencial. The Economist dedica un artículo al nuevo sector que Mighty Homes y su competidor más obvio en el mercado residencial californiano y eventualmente estadounidense, Palari Homes, tratan de acelerar con una estrategia más propia de firmas tecnológicas que de constructoras.
Las impresoras para construcción adaptadas por Palari Homes, Mighty Buildings y sus alternativas en Europa (la constructora Weber Saint-Gobain asiste en la «impresión» de un barrio residencial pionero en la ciudad holandesa de Eindhoven, Project Milestone), extruden un compuesto que se solidifica con rapidez al aplicar sobre él una luz ultravioleta que parte del mismo cabezal que describe el recorrido numérico programado. Gracias a la rapidez de secado de los compuestos empleados, estas compañías pueden imprimir aleros o techos sin usar moldes de soporte.
En Europa, el barrio pionero Project Milestone, coordinado por la Universidad Tecnológica de Eindhoven, se compone de las primeras casas impresas destinadas al alquiler subvencionado. Los nuevos inquilinos recibieron la llave de las viviendas impresas el 30 de julio.
No muy lejos de allí, en la localidad belga de Westerlo, se erige la primera casa impresa de una sola pieza, y no a partir de módulos ensamblados después de su impresión por separado. Esta vivienda, Kamp C, cuenta con dos plantas, tiene una superficie de 90 metros cuadrados, climatización radiante integrada en techo y suelos, así como prestaciones bioclimáticas.
Impacto y rendimiento de estructuras impresas
Estas firmas y proyectos experimentales reciben ahora el interés de la prensa que acaparó hasta hace poco Katerra, la firma que trató de crear un método propio de construcción modular con madera laminada de gran resistencia (CLT en sus siglas en inglés) y aplicarlo a gran escala con una estrategia de expansión a golpe de crédito que la llevó recientemente a declarar la bancarrota.
Katerra aspiró a convertirse en el «unicornio» de la construcción prefabricada en un mercado donde es muy difícil anteponer la innovación (por ejemplo, en las prestaciones y el rendimiento de los materiales, o en el uso de técnicas modulares) a los costes y a la propia dinámica que mecanismos de financiación, ordenación del suelo y constructores imponen.
La apuesta de empresas como Mighty Buildings o Palari Homes parece, si cabe, más arriesgada, y pretende reducir el uso de operarios humanos por un proceso robotizado similar al que fordismo y toyotismo impusieron en el sector automovilístico.
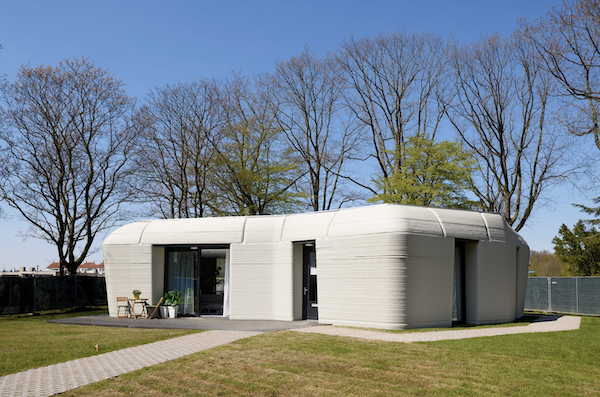
Quienes consideran que las casas impresas bajo demanda son una idea excéntrica o simplemente irrealizable, quizá deban recordar el inicio de otros procesos que parecían igualmente ajenos a cualquier transformación profunda. La novedad no estriba tanto en la posibilidad de construir una casa en 24 horas, sino en el hecho de que el edificio se materializa usando una impresora aditiva y, potencialmente, usando compuestos locales de origen mineral y vegetal (a menudo, procedente de desechos o plantas que combinen el secuestro de CO2 y el rendimiento bioclimático).
Un compuesto sostenible para impresoras de construcción
En la localidad de Massa Lombardo, Emilia-Romagna, Italia, la empresa Wasp ha puesto a prueba sus equipos con una casa impresa con un compuesto a base de suelo local y desechos agrarios. La vivienda es biodegradable y puede volver al entorno al final de su vida útil o si dejara de mantenerse, tal y como ocurriría con técnicas de construcción tradicionales.
Si bien las nuevas firmas de impresión de viviendas dependen de compuestos a base de piedra caliza (cuya transformación en óxido de calcio y dióxido de carbono es responsable del 8% de las emisiones antropogénicas), las nuevas combinaciones prometen prescindir eventualmente de esta materia prima.
Un equipo de la Universidad de Texas dirigido por Sarbajit Banerjee se ha inspirado en trabajos previos en la construcción de carreteras en áreas remotas de Alberta, en Canadá, para dar con una pasta que combina suelo y fibras de madera con silicatos líquidos o solubles en agua. Una vez aplicado, el compuesto resultante logra prestaciones similares al cemento.
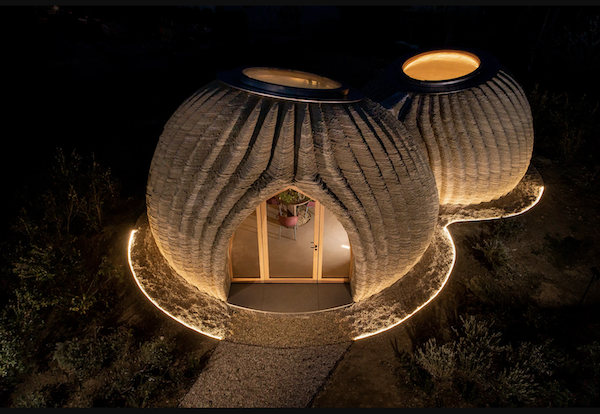
Varios proyectos comparten características esenciales con los mencionados, si bien lo que parecía una técnica experimental alejada de la realidad del mercado aprovecha ahora la confluencia de varios fenómenos: un mercado de la vivienda súbitamente al alza en el mundo desarrollado a raíz de la inflación en plena reactivación económica tras la pandemia; el interés por reducir el impacto y las emisiones en construcción residencial; y la escasez de mano de obra en regiones como la Costa Oeste de Estados Unidos.
¿Próximamente?
En este contexto, Mighty Buildings asegura requerir únicamente el 5% de la mano de obra tradicional, acortar dramáticamente el tiempo de construcción, y reducir el impacto derivado del transporte de materias primas y otros procesos asociados a la construcción tradicional (Palari Homes estima que el ahorro en transporte reduce 2 toneladas de emisiones de CO2).
Otra de las empresas del sector, 14Trees (proyecto conjunto entre la cementera Holcim y una incubadora de negocios británica), asegura ultimar un proceso de fabricación capaz de imprimir la estructura de una vivienda en 12 horas por un coste inferior a 10.000 dólares.
Mientras tanto, en México la firma Icon colabora en el proyecto de la ONG New Story para imprimir viviendas de 46 m2 destinadas a personas sin hogar, cuyos componentes son ensamblados por voluntarios de la organización Échale.
Durante nuestra visita a Mighty Homes, su consejero delegado nos explicaba uno de los escollos que afronta la nueva técnica: la ausencia de referentes dificulta la certificación administrativa de las nuevas estructuras y los códigos de edificación deberán adaptarse sobre la marcha.
Llegan, sin embargo, las primeras certificaciones que permiten construir casas impresas en Alemania, Dinamarca, Oriente Medio (existen proyectos en Dubai y Arabia Saudí), India o Estados Unidos.
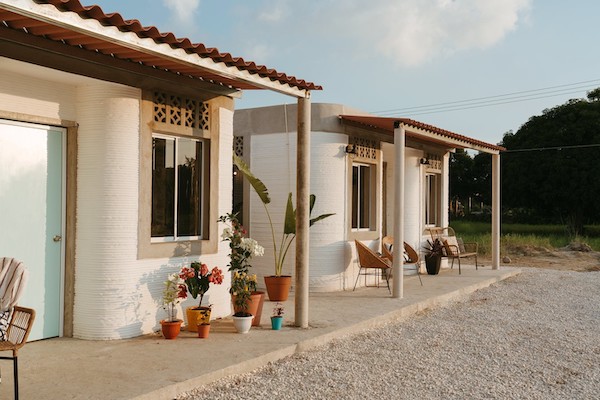
Varios de los actores del sector son optimistas sobre el futuro de una técnica que podría facilitar la colonización de la luna y Marte. Quizá no haga falta esperar demasiado tiempo para comprobar si las casas impresas son capaces de proliferar en barrios más cercanos.